Wet limestone gypsum flue gas desulfurization technology
Wet limestone gypsum flue gas desulfurization technology
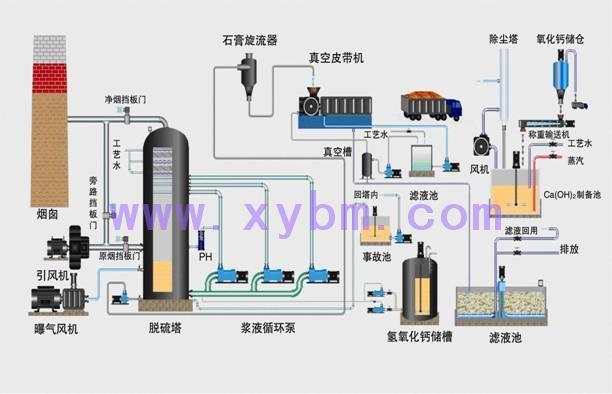
Process flow chart of limestone gypsum flue gas desulfurization technology
Process characteristics:
With simple process flow,advanced and reliable technology,it is the most widely used desulfurization process at home and abroad.
The absorption tower is an empty tower spray with multi-layer spray layer,advanced and reliable nozzle and oxidized air pipe.
The process has a wide range of flue gas treatment,and the flue gas of 200MW~600MW units can be effectively treated.
The fuel has strong adaptability in sulfur range,which can meet the stable operation of the unit within the load range of 30%-110%;It is especially suitable for projects with high sulfur coal and Low SO2 emission in key areas.
Desulfurization efficiency is generally greater than 90%,up to 99%.
The unique air flow homogenization device makes the flue gas entering the absorption tower evenly distributed,strengthens the turbulence degree of flue gas and washing liquid,and improves the desulfurization efficiency.
The process has advanced economic and technical indicators.When limestone is used as desulfurizer,the liquid gas ratio is 10~12l/m3,and the energy consumption of the desulfurization system is low;High utilization rate of absorbent:calcium sulfur ratio 1.02~1.03.
The desulfurization liquid dosing device at the bottom of the tower is uniformly distributed with multiple suspension nozzles,and the bottom of the large-diameter absorption tower will not produce sedimentation.
The anti-corrosion materials inside the absorption tower are corrosion-resistant,wear-resistant and durable.
The flue gas desulfurization system is fully automated.
Process system composition:
Flue gas system SO2 absorption system→absorbent preparation system→gypsum dehydration,storage and transportation system→wastewater treatment system→process water system→compressed air and steam system→electrical control system→slurry discharge system
Scope of application:
Medium and large new or renovation projects
The sulfur content of coal is 0.5%-5%,up to 8%
Desulfurization efficiency shall be above 95%
Areas with rich limestone resources and extensive comprehensive utilization of gypsum
Double alkali flue gas desulfurization technology
With simple process flow,advanced and reliable technology,it is the most widely used desulfurization process at home and abroad.
The absorption tower is an empty tower spray with multi-layer spray layer,advanced and reliable nozzle and oxidized air pipe.
The process has a wide range of flue gas treatment,and the flue gas of 200MW~600MW units can be effectively treated.
The fuel has strong adaptability in sulfur range,which can meet the stable operation of the unit within the load range of 30%-110%;It is especially suitable for projects with high sulfur coal and Low SO2 emission in key areas.
Desulfurization efficiency is generally greater than 90%,up to 99%.
The unique air flow homogenization device makes the flue gas entering the absorption tower evenly distributed,strengthens the turbulence degree of flue gas and washing liquid,and improves the desulfurization efficiency.
The process has advanced economic and technical indicators.When limestone is used as desulfurizer,the liquid gas ratio is 10~12l/m3,and the energy consumption of the desulfurization system is low;High utilization rate of absorbent:calcium sulfur ratio 1.02~1.03.
The desulfurization liquid dosing device at the bottom of the tower is uniformly distributed with multiple suspension nozzles,and the bottom of the large-diameter absorption tower will not produce sedimentation.
The anti-corrosion materials inside the absorption tower are corrosion-resistant,wear-resistant and durable.
The flue gas desulfurization system is fully automated.
Process system composition:
Flue gas system SO2 absorption system→absorbent preparation system→gypsum dehydration,storage and transportation system→wastewater treatment system→process water system→compressed air and steam system→electrical control system→slurry discharge system
Scope of application:
Medium and large new or renovation projects
The sulfur content of coal is 0.5%-5%,up to 8%
Desulfurization efficiency shall be above 95%
Areas with rich limestone resources and extensive comprehensive utilization of gypsum
Double alkali flue gas desulfurization technology
Process characteristics:
1.Mature technology,stable and reliable operation.The failure rate of main equipment and equipment is low,so it will not affect the safe operation of the boiler due to the failure of desulfurization equipment.
2.Advanced technology and low operation cost.Because the sodium alkali activity is very strong and extremely high,only a very low liquid gas ratio can achieve high efficiency desulfurization effect;Because of the low-cost calcium alkali regeneration and sodium alkali reuse,the operation cost is greatly reduced.
3.The project has low investment and high economic benefit.The project investment of sodium calcium double alkali method is only 2/3~3/4 of that of other wet methods;The desulfurization efficiency also reaches 90%~95%,and the SO2 and soot emissions after desulfurization fully meet the environmental protection requirements.
4.It has strong adaptability to the change of coal type.Sodium alkali liquor is used as desulfurizer,which has good process absorption effect and high utilization rate of absorbent.Factors such as pH value and liquid gas ratio can be properly adjusted according to the change of boiler coal to ensure the realization of design desulfurization rate.
5.Integration of desulfurization and dust removal.Through spraying,absorption,adsorption,regeneration and other physical and chemical processes,as well as dehydration and demisting,the purpose of desulfurization,dust removal,dehumidification and flue gas purification is achieved.
6.The effect of saving energy,water and desulfurizer is remarkable.The double alkali method has the characteristics of"high desulfurization efficiency,high availability,high reliability,low investment cost,low operation cost and small floor area".
7.NaOH(Na2CO3)is used for desulfurization.The desulfurization solution is mainly NaOH(Na2CO3)aqueous solution.During the circulation process,there is no corrosion,scouring or blockage to the water pump,pipeline and equipment,which is convenient for equipment operation and maintenance.
8.The sodium based absorption liquid reacts quickly to SO2,so it has a small liquid gas ratio to achieve high desulfurization efficiency.The unique tower design increases the contact area and contact time between the desulfurization liquid and flue gas,thus improving the desulfurization efficiency,generally≥95%.
9.The regeneration of desulfurizer and desulfurizing precipitation occur outside the tower body to avoid blockage and wear in the tower,improve the reliability of operation and reduce the operation cost.
10.With the empty tower spray as the desulfurization tower structure,the tower resistance is small,the operation reliability is high,and the accident rate is low.
11.Calcium based replacement and sodium based regeneration cycle can improve the utilization rate of lime.Sodium alkali is involved in the reaction,and the actual consumption is calcium alkali.Sodium alkali is recycled,and the consumption of sodium alkali is less than 1%.
Process system composition:
Flue gas system→SO2 absorption system→absorbent preparation and supply system→gypsum dehydration system→process water system→electric control system.
Scope of application:
Wide range of application,suitable for low,medium and high sulfur coal smoke;
It is especially suitable for flue gas desulfurization technology of small and medium-sized boilers and has a broad market prospect.
Ammonia flue gas desulfurization technology
Ammonia desulfurization uses liquid ammonia or ammonia water to remove SO2 from flue gas and generate by-product ammonium sulfate
1.Mature technology,stable and reliable operation.The failure rate of main equipment and equipment is low,so it will not affect the safe operation of the boiler due to the failure of desulfurization equipment.
2.Advanced technology and low operation cost.Because the sodium alkali activity is very strong and extremely high,only a very low liquid gas ratio can achieve high efficiency desulfurization effect;Because of the low-cost calcium alkali regeneration and sodium alkali reuse,the operation cost is greatly reduced.
3.The project has low investment and high economic benefit.The project investment of sodium calcium double alkali method is only 2/3~3/4 of that of other wet methods;The desulfurization efficiency also reaches 90%~95%,and the SO2 and soot emissions after desulfurization fully meet the environmental protection requirements.
4.It has strong adaptability to the change of coal type.Sodium alkali liquor is used as desulfurizer,which has good process absorption effect and high utilization rate of absorbent.Factors such as pH value and liquid gas ratio can be properly adjusted according to the change of boiler coal to ensure the realization of design desulfurization rate.
5.Integration of desulfurization and dust removal.Through spraying,absorption,adsorption,regeneration and other physical and chemical processes,as well as dehydration and demisting,the purpose of desulfurization,dust removal,dehumidification and flue gas purification is achieved.
6.The effect of saving energy,water and desulfurizer is remarkable.The double alkali method has the characteristics of"high desulfurization efficiency,high availability,high reliability,low investment cost,low operation cost and small floor area".
7.NaOH(Na2CO3)is used for desulfurization.The desulfurization solution is mainly NaOH(Na2CO3)aqueous solution.During the circulation process,there is no corrosion,scouring or blockage to the water pump,pipeline and equipment,which is convenient for equipment operation and maintenance.
8.The sodium based absorption liquid reacts quickly to SO2,so it has a small liquid gas ratio to achieve high desulfurization efficiency.The unique tower design increases the contact area and contact time between the desulfurization liquid and flue gas,thus improving the desulfurization efficiency,generally≥95%.
9.The regeneration of desulfurizer and desulfurizing precipitation occur outside the tower body to avoid blockage and wear in the tower,improve the reliability of operation and reduce the operation cost.
10.With the empty tower spray as the desulfurization tower structure,the tower resistance is small,the operation reliability is high,and the accident rate is low.
11.Calcium based replacement and sodium based regeneration cycle can improve the utilization rate of lime.Sodium alkali is involved in the reaction,and the actual consumption is calcium alkali.Sodium alkali is recycled,and the consumption of sodium alkali is less than 1%.
Process system composition:
Flue gas system→SO2 absorption system→absorbent preparation and supply system→gypsum dehydration system→process water system→electric control system.
Scope of application:
Wide range of application,suitable for low,medium and high sulfur coal smoke;
It is especially suitable for flue gas desulfurization technology of small and medium-sized boilers and has a broad market prospect.
Ammonia flue gas desulfurization technology
Ammonia desulfurization uses liquid ammonia or ammonia water to remove SO2 from flue gas and generate by-product ammonium sulfate
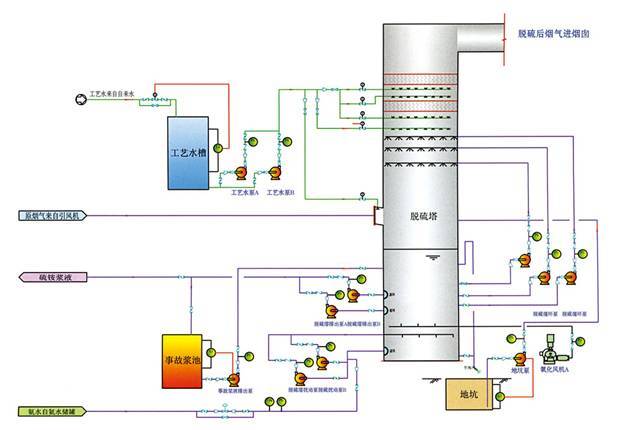
Process flow chart of ammonia flue gas desulfurization technology
Process characteristics:
The system is closed-circuit circulation,without secondary waste residue,waste water and waste gas pollution;
The desulfurization efficiency is greater than 95%and the amount of water mist is less than 75mg/nm3
High utilization rate of absorbent,and the desulfurization tower is not easy to scale
Ammonia method has strong adaptability to sulfur content in coal,especially suitable for flue gas desulfurization of high sulfur coal;
Turn waste into treasure,and the by-product of desulfurization is ammonium sulfate fertilizer,so as to maximize the value of SO2 recovery.The market potential of ammonium sulfate fertilizer is huge
The system has the advantages of low operation cost,short process,convenient and reliable operation and low energy consumption,which is only 50%of that of limestone gypsum method
Process system composition:
Electrical control system of desulfurization washing system,flue gas system,ammonia storage and transportation system,ammonium sulfate production system,process water system,compressed air system
Scope of application:
Ammonia desulfurization has strong adaptability to the sulfur content in coal,and the desulfurization of coal with low,medium and high sulfur content can adapt.
It is especially suitable for desulfurization of medium and high sulfur coal.The higher the sulfur content in coal,the greater the output of desulfurization by-product ammonium sulfate and the higher the economy.
Applicable to large and medium-sized new or modified units
Desulfurization efficiency is required to be above 95%
Applicable to coal chemical and petrochemical enterprises
The system is closed-circuit circulation,without secondary waste residue,waste water and waste gas pollution;
The desulfurization efficiency is greater than 95%and the amount of water mist is less than 75mg/nm3
High utilization rate of absorbent,and the desulfurization tower is not easy to scale
Ammonia method has strong adaptability to sulfur content in coal,especially suitable for flue gas desulfurization of high sulfur coal;
Turn waste into treasure,and the by-product of desulfurization is ammonium sulfate fertilizer,so as to maximize the value of SO2 recovery.The market potential of ammonium sulfate fertilizer is huge
The system has the advantages of low operation cost,short process,convenient and reliable operation and low energy consumption,which is only 50%of that of limestone gypsum method
Process system composition:
Electrical control system of desulfurization washing system,flue gas system,ammonia storage and transportation system,ammonium sulfate production system,process water system,compressed air system
Scope of application:
Ammonia desulfurization has strong adaptability to the sulfur content in coal,and the desulfurization of coal with low,medium and high sulfur content can adapt.
It is especially suitable for desulfurization of medium and high sulfur coal.The higher the sulfur content in coal,the greater the output of desulfurization by-product ammonium sulfate and the higher the economy.
Applicable to large and medium-sized new or modified units
Desulfurization efficiency is required to be above 95%
Applicable to coal chemical and petrochemical enterprises
Magnesium flue gas desulfurization technology
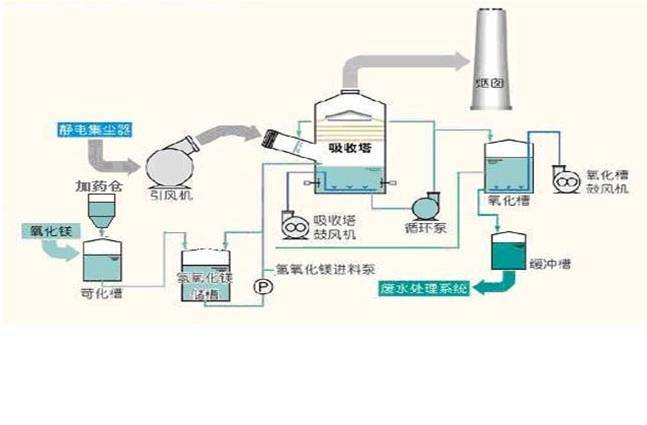
Process characteristics:
1.Mature technology
2.Sufficient sources of raw materials
3.High desulfurization efficiency,and the desulfurization efficiency can reach more than 95%
4.The investment cost is less.Compared with calcium desulfurization,the investment cost of the same desulfurization system can be reduced by more than 50%.
5.Low operation cost.The amount of magnesium oxide used to remove the same SO2 is 40%of calcium carbonate,and the liquid gas ratio is below 5l/m3.
6.Reliable operation,no equipment scaling and blockage,and safe and effective operation of the whole desulfurization system without secondary pollution.
7.The comprehensive benefit is high,and the utilization prospect of by-products is broad.
System composition:
Flue gas system,SO2 absorption system,desulfurizer slurry preparation system,by-product treatment system,accident slurry system and process water system
Scope of application:
It is applicable to large and medium-sized new or renovation projects,and can handle large amount of flue gas.
Widely used in power industry,metallurgical sintering machine flue gas,industrial boilers,paper mills and other desulfurization projects.
Selective Catalytic Reduction
1、Selective catalytic reduction technology(SCR)
Selective catalytic reduction(SCR)denitration technology means that under the action of catalyst,the reducing agent(liquid ammonia)reacts with nitrogen oxides in flue gas to generate harmless nitrogen and water,so as to remove NOx in flue gas.Selectivity means that the reducing agent NH3 reacts with NOx in flue gas instead of with oxygen in flue gas.
1.Mature technology
2.Sufficient sources of raw materials
3.High desulfurization efficiency,and the desulfurization efficiency can reach more than 95%
4.The investment cost is less.Compared with calcium desulfurization,the investment cost of the same desulfurization system can be reduced by more than 50%.
5.Low operation cost.The amount of magnesium oxide used to remove the same SO2 is 40%of calcium carbonate,and the liquid gas ratio is below 5l/m3.
6.Reliable operation,no equipment scaling and blockage,and safe and effective operation of the whole desulfurization system without secondary pollution.
7.The comprehensive benefit is high,and the utilization prospect of by-products is broad.
System composition:
Flue gas system,SO2 absorption system,desulfurizer slurry preparation system,by-product treatment system,accident slurry system and process water system
Scope of application:
It is applicable to large and medium-sized new or renovation projects,and can handle large amount of flue gas.
Widely used in power industry,metallurgical sintering machine flue gas,industrial boilers,paper mills and other desulfurization projects.
Selective Catalytic Reduction
1、Selective catalytic reduction technology(SCR)
Selective catalytic reduction(SCR)denitration technology means that under the action of catalyst,the reducing agent(liquid ammonia)reacts with nitrogen oxides in flue gas to generate harmless nitrogen and water,so as to remove NOx in flue gas.Selectivity means that the reducing agent NH3 reacts with NOx in flue gas instead of with oxygen in flue gas.

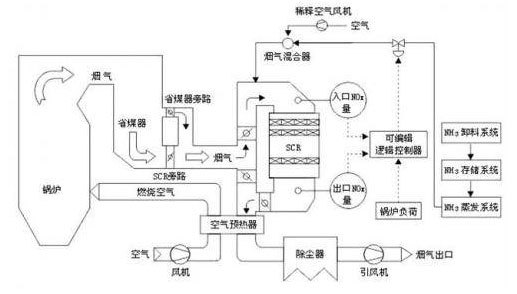
Selective catalytic reduction denitration (SCR) process flow chart
Process characteristics:
High denitration efficiency,up to 85%-90%
The denitration device operates stably and reliably with high equipment utilization rate
Long service life of catalyst,up to 24000 hours
NH3 escape rate≤5ppm
The SCR reaction device is arranged behind the boiler economizer without affecting the boiler structure and performance
System composition:
SCR reactor/catalyst system→flue gas system→ammonia storage,preparation and supply system→ammonia injection system→ammonia/air mixing system→soot blowing system→SCR control system
2、Selective non catalytic reduction technology(SNCR)
SNCR uses NH3,urea and other reducing agents to inject into the furnace for selective reaction with NOx without catalyst.The reductant is injected into the area with furnace temperature of 850~1050℃.The reductant(ammonia or urea)is rapidly thermally decomposed into NH3 and reacts with NOx in the flue gas to generate N2.This method uses the furnace as the reactor.
High denitration efficiency,up to 85%-90%
The denitration device operates stably and reliably with high equipment utilization rate
Long service life of catalyst,up to 24000 hours
NH3 escape rate≤5ppm
The SCR reaction device is arranged behind the boiler economizer without affecting the boiler structure and performance
System composition:
SCR reactor/catalyst system→flue gas system→ammonia storage,preparation and supply system→ammonia injection system→ammonia/air mixing system→soot blowing system→SCR control system
2、Selective non catalytic reduction technology(SNCR)
SNCR uses NH3,urea and other reducing agents to inject into the furnace for selective reaction with NOx without catalyst.The reductant is injected into the area with furnace temperature of 850~1050℃.The reductant(ammonia or urea)is rapidly thermally decomposed into NH3 and reacts with NOx in the flue gas to generate N2.This method uses the furnace as the reactor.
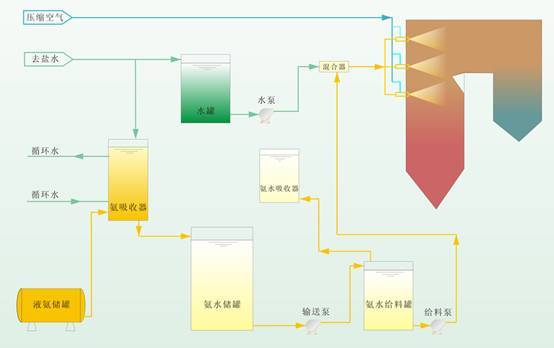
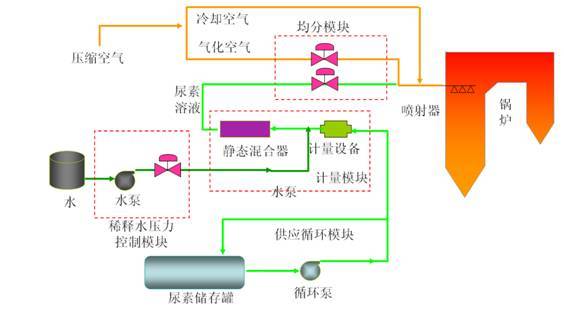
Process flow chart of selective non catalytic reduction denitration (SNCR)
Process characteristics:
The floor area is small and no additional reactor is required.The boiler furnace is used as the reactor,and the reaction temperature is 850~1050℃;
The denitration efficiency can reach 40~70%;
Do not use catalyst,do not produce so2/so3 oxidation,and do not cause blockage or corrosion of air preheater;
NH3 escape 5~10ppm;
No new pressure loss of smoke and air system;
The fuel can be changed at will without affecting the denitration efficiency
The operation cost is low.When the retrofit efficiency of existing boiler denitration technology is low,the economy of SNCR denitration technology is high;
SNCR is suitable for the transformation of old power plants.It is an economic and practical denitration technology and suitable for China's national conditions
System composition:
Ammonia solution preparation and storage system,reductant dilution and metering system,reductant distribution system,reductant injection system,compressed air system,process water system and electrical control system
The floor area is small and no additional reactor is required.The boiler furnace is used as the reactor,and the reaction temperature is 850~1050℃;
The denitration efficiency can reach 40~70%;
Do not use catalyst,do not produce so2/so3 oxidation,and do not cause blockage or corrosion of air preheater;
NH3 escape 5~10ppm;
No new pressure loss of smoke and air system;
The fuel can be changed at will without affecting the denitration efficiency
The operation cost is low.When the retrofit efficiency of existing boiler denitration technology is low,the economy of SNCR denitration technology is high;
SNCR is suitable for the transformation of old power plants.It is an economic and practical denitration technology and suitable for China's national conditions
System composition:
Ammonia solution preparation and storage system,reductant dilution and metering system,reductant distribution system,reductant injection system,compressed air system,process water system and electrical control system
desulfurization,system,flue